Composite carbide solution powder is a composite material composed of 77% tantalum carbide (TaC) and 23% niobium carbide (NbC). The high hardness, melting point, and thermal stability of carbides make it an ideal choice for applications that require materials to operate under harsh conditions.
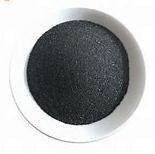
Composite carbide solution powder
Tantalum is a metallic element with an atomic number of 73 and a chemical symbol of Ta. It belongs to the VB group of elements, and its corresponding elemental form is a steel-gray metal. It mainly exists in tantalum iron ore and often coexists with niobium. The carbides of tantalum mainly include Ta2C and TaC, and Ta2C has two isomers, α – Ta2C and β – Ta2C. TaC is a dark brown powder with a melting point of 3880 ℃, a boiling point of 5500 ℃, and a density of 14.4g/cm3. It has good chemical stability and can only be dissolved in mixed solutions of nitric acid and hydrofluoric acid. Tantalum carbides are difficult to oxidize in air at temperatures below 1000-1100 ℃ and are classified as hard compounds that are difficult to melt. Under the action of nitrogen or ammonia, nitrides are easily generated. Tantalum carbide is mainly used in hard alloys because tantalum has extremely strong corrosion resistance. Tantalum carbide can improve the hardness, strength, and melting point of cutting tools and grinding tools. However, due to the high cost of tantalum carbide, tantalum niobium composite carbide is often used abroad to replace single tantalum carbide.
Niobium carbide is a compound composed of niobium and carbon, usually represented by the chemical formula NbC. It is a material with high hardness and high melting point. The high hardness of niobium carbide makes it suitable for manufacturing wear-resistant parts and tools, such as cutting tools and other applications that require high durability. Its high melting point (approximately above 3600 ° C) allows it to maintain its structural integrity in high-temperature environments without melting or deforming, making it suitable for thermal protection systems in aerospace or refractory materials in metal processing. Niobium carbides are inert to most chemicals and do not easily react with them, exhibiting excellent performance in corrosive environments. Despite being a ceramic material, niobium carbide still has certain electrical and thermal conductivity. These characteristics make it suitable for use in electronic components.
The Effect of TaC (NbC) on the Properties of Hard Alloys
- Adding TaC can improve the heat resistance, high-temperature hardness, and high-temperature strength of hard alloys, as well as enhance their oxidation resistance. Adding a small amount of TaC to WC Co hard alloys can improve their high-temperature hardness and strength at 800 ° C, with a maximum increase in strength of about 15-30kg/square meter. If NbC is added, the maximum bending strength at 800 ° C is increased by about 10-25kg/square meter. After adding TaC to WC TiC Co hard alloys, the high-temperature hardness can be increased by 50-100HV. Although adding NbC can also improve the high-temperature hardness of such hard alloys, the effect is not significant compared to adding TaC. In addition, TaC and NbC can also increase the bonding temperature between these hard alloys and steel, slowing down the diffusion of hard alloy components into the steel.
- Adding TaC to WC Co hard alloys can significantly improve their room temperature hardness and wear resistance. Adding TaC can increase the voltage by 40-100HV, and adding NbC can increase the voltage by 70-150HV. Adding TaC to WC TiC Co hard alloys can improve their resistance to crescent wear and back-cutting wear. TaC or NbC has no significant effect on the room temperature hardness of this type of hard alloy.
- Adding TaC to WC TiC Co hard alloys can improve their bending strength (adding 4%~6% TaC can increase strength by 12%~18%) and impact toughness. When the total content of TiC and TaC in the hard alloy remains constant, its bending strength and impact toughness increase with the increase of TaC, as shown in the figure. However, when TaC or NbC is added to WC Co hard alloys, their bending strength and impact toughness are slightly reduced. TaC can significantly improve the fatigue strength of WC TiC Co hard alloys, and its fatigue strength also increases with the increase of TaC content.
- TaC and NbC can refine the grain size, with NbC showing a more significant effect, which helps to improve the wear resistance and resistance to crescent wear of hard alloys. TaC also helps to reduce friction factors, thereby lowering cutting temperatures.
- After adding a large amount of TaC (12%~15%) to hard alloys, their ability to resist crack formation (thermal vibration resistance) and plastic deformation during periodic temperature changes can be increased, making them suitable for milling without easily producing chipping.
Supplier
Metalinchina is a trusted global chemical material supplier & manufacturer with over 12 years experience in providing super high-quality metals and metal alloy. The company export to many countries, such as USA, Canada,Europe,UAE,South Africa, etc. As a leading nanotechnology development manufacturer, Metalinchina dominates the market. Our professional work team provides perfect solutions to help improve the efficiency of various industries, create value, and easily cope with various challenges. If you are looking for high quality TaC Powder, please feel free to contact us(nanotrun@yahoo.com)